Automotive restoration and customization
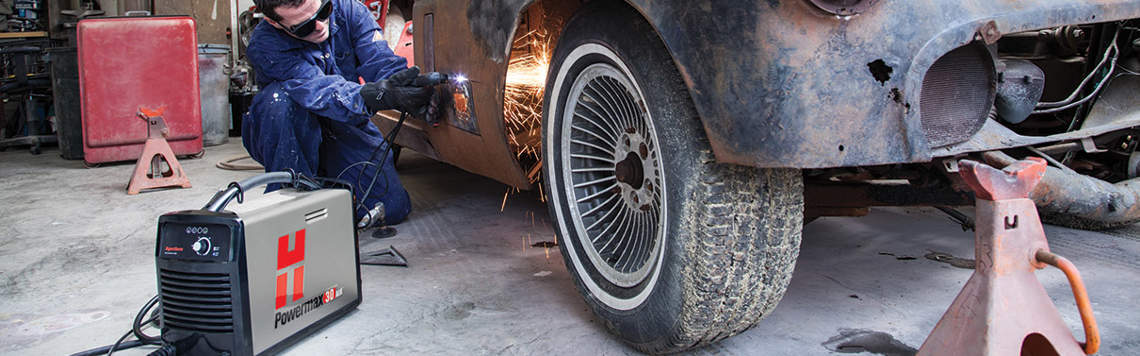
Garages, custom shops, and hobbyists use Hypertherm air plasma systems to easily cut metal when restoring or customizing cars and trucks.
Overview
Hobbyists and professionals alike appreciate the portability and ability of Powermax® plasma to cut or gouge any type of metal – including dirty, rusted, and painted parts.
Unique Hypertherm products such as our 15-degree torch and HyAccess® consumables make it easy to cut hard to reach areas such as inside engine compartments, behind angled bumpers, or in tire wells. FlushCut™ consumables are ideal for rusty bolt and exhaust removal with minimal grinding.
Typical uses include:
-
Cutting out rusted body parts or other metal
-
Fabricating new parts or frame sections
-
Removing rusted nuts and bolts
-
Preparing cracked parts for welding
Explore automotive restoration solutions
Plasma bevel cutting
Bevel cutting is cutting a part with an edge not perpendicular to the top of the piece. It is typically used to prepare plates or pipes for welding. Bevels can be cut at different angles and configurations, resulting in varying edge profiles.
Extended reach cutting
Hypertherm’s HyAccess® extended reach consumables give users extra reach when plasma cutting or gouging in hard to access or confined spaces, and are designed for use with Powermax air plasma systems.
Plasma flush cutting
FlushCut® consumables for Powermax® systems allow easy removal of protrusions, welded attachments, bolts, and fixtures from metal surfaces without cutting into the base material.
Plasma gouging
Plasma gouging – removing metal using a plasma arc – is similar to plasma cutting. A plasma arc between the torch and the workpiece melts the metal, and a gas jet blows away the molten material.
Plasma hole cutting
Many fabrication processes require cutting holes to bolt two or more pieces or parts together, so hole production is an important part of most cutting operations. Multiple holes can be cut into a large plate, pipe, or drum with plasma.
Plasma marking
Marking metal to indicate bend or score lines, inventory numbers, or reference points for drilling or robotic processes is traditionally done with a hammer and punch, powder or ink, soapstone, or handheld engraving machines. Using plasma for marking during CNC processes offers many significant advantages.
Temporary attachment removal
Flush cutting with Powermax® plasma systems lets you cut closer to base materials than ever before, reducing costly, time consuming secondary operations. Cleaner cuts with less damage to the base metal saves costs in reusable temporary attachments.