Platesaver technology helps increase productivity and profitability
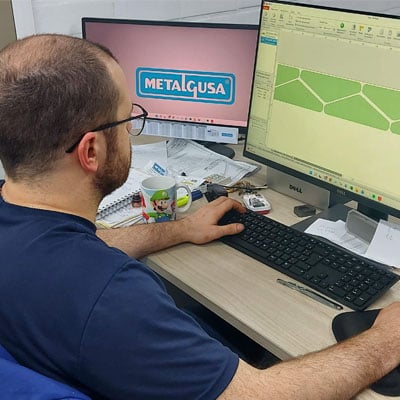
Company overview: Metalgusa
Metalgusa is a steel service center in Southern Brazil. The company works with a wide variety of customers and specializes in carbon steel, mostly between 16 mm (.625 inch) and 25 mm (1 inch) thick. The company prides itself on operational excellence and has been offering intelligent solutions that guarantee a high standard of quality, technology, and reliability in steel cutting operating for almost four decades. Metalgusa works to deliver high-quality parts that meet or exceed customer specifications for cut quality and are delivered on-time and on-budget. One way it does this is using plasma equipment and software technology from Hypertherm Associates.
Challenge: Current plasam cutting systems could not keep up with demand
Two Hypertherm plasma systems, an HPR260XD® and HPR400XD®, did the bulk of Metalgusa’s plasma cutting for years. With business growing, Metalgusa needed to add a third system to keep up with demand.
Solution: XPR300 increases capacity and efficiency
Happy with its two HPR systems, the company didn’t hesitate to choose another Hypertherm plasma system, this time choosing a 300-amp X-Definition® system, the XPR300®. To get the most out of the XPR300, Metalgusa added Hypertherm’s ProNest® nesting software with PlateSaver™ technology and True Hole® technology.
The XPR300
The XPR300 represents the most significant advance in mechanized plasma cutting technology, redefining what plasma can do by expanding its capabilities and opportunities in ways never before possible. With unmatched X-Definition cut quality on mild steel, stainless steel, and aluminum, the XPR300 increases cut speed, dramatically improves productivity, and reduces operating costs.
New ease-of-use features and engineered system optimization make the XPR300 easier to run with minimal operator intervention, while also ensuring optimal performance and unmatched reliability. Advanced power supply technology delivers highly responsive, rapid system feedback, and automatically intervenes to eliminate events that negatively impact system efficiency and consumable life.
-
Significantly reduced operating costs than previous generation technology
-
Increased cut speeds on thicker materials
-
Thicker piercing capability than competitive plasma systems
-
Increased consumable life to up to 3 times that of competitor’s systems by eliminating the impact of ramp down errors
-
Elimination of catastrophic electrode blowouts which can damage the torch at high current levels
ProNest nesting software
ProNest nesting software for advanced mechanized cutting is designed to supercharge cutting operations, enabling greater automation, efficiency, and profitability. ProNest optimizes performance for plasma, laser, waterjet, and oxyfuel cutting machines.
ProNest’s high-yield nesting reduces material costs and increases profitability. Intuitive screens and a wide variety of helpful features make it easy to learn and use. Its faster, fully automated interface can reduce programing time from hours to minutes, while specialized cutting techniques can reduce total cut time by up to 50%.
SureCut technologies
SureCut is designed to maximize cutting performance by automatically applying optimized cutting process parameters to simplify cutting and reduce operator intervention. SureCut is delivered through a combination of Hypertherm products such as automated systems, CNCs, and CAM software.
SureCut technologies include:
-
PlateSaver™ technology combines XPR arc stability and specialized software parameters to dramatically increase material utilization.
-
True Hole® technology applies process expertise to automatically deliver bolt ready holes.
-
True Bevel™ technology automatically applies the correct bevel angle and reduces operator trial and error.
-
Rapid Part™ technology increases the number of parts produced per hour by automatically reducing cut-to-cut cycle time between parts.
True Hole technology
True Hole technology produces significantly better hole quality than what was previously possible using plasma. True Hole virtually eliminates hole taper and reduces ding, delivering true bolt hole quality automatically, without operator intervention.
True Hole is automatically applied by the nesting software or CNC software to thicknesses up to 25 mm (1 inch) diameter and hole coverage ranges from hole diameter to thickness ratios from 2:1 to as low as 1:1.
Business impact: XPR300 increases material utilization, productivity, and profits
“To get the most out of our investment in the XPR system, we started using ProNest with PlateSaver technology. Immediately, our standard of service rose considerably. The Hypertherm solution in general has given us several benefits.” – Patrick Bernardo da Silva, Programming Manager, Metalgusa
With the addition of a third plasma cutting system, Metalgusa gained cutting capacity and can now process more work, and the company soon discovered that it gained more than just additional capacity. By combining the XPR plasma system with Hypertherm’s ProNest nesting software and PlateSaver, Metalgusa has significantly increased material utilization. Da Silva is thrilled with the PlateSaver technology, since it helps Metalgusa fit more parts on each plate.
“In this last project, for example, we went from 224 pieces cut per plate, to 247 pieces cut; the software reduced lead length from 11 to 8 millimeters in a 16 mm plate at 220 amps. With the high cost of material, we increased profitability. We were able to make more parts with the same sheet, with higher quality and less waste.” – Patrick Bernardo da Silva, Programming Manager, Metalgusa
In addition, Metalgusa is taking advantage of True Hole to produce very accurate holes, which helps deliver higher quality parts to customers without the need for secondary hole cutting processes.
Da Silva says the combination of the Hypertherm XPR plasma system and ProNest software is helping it produce higher quality parts, more quickly, without the need for time-consuming and costly secondary work.
Our plasma cut parts are virtually ready-to-use with no rework required, so we’ve had numerous gains.
Patrick Bernardo da Silva, Programming Manager
Metalgusa
Learn how the XPR300 can help your business strike the perfect balance between cut quality, cut speed, and cost. Click the button below, fill out the form, and a Hypertherm product expert will contact you.
Learn more about Platesaver technology