Plasma cutting vs. fiber laser cutting
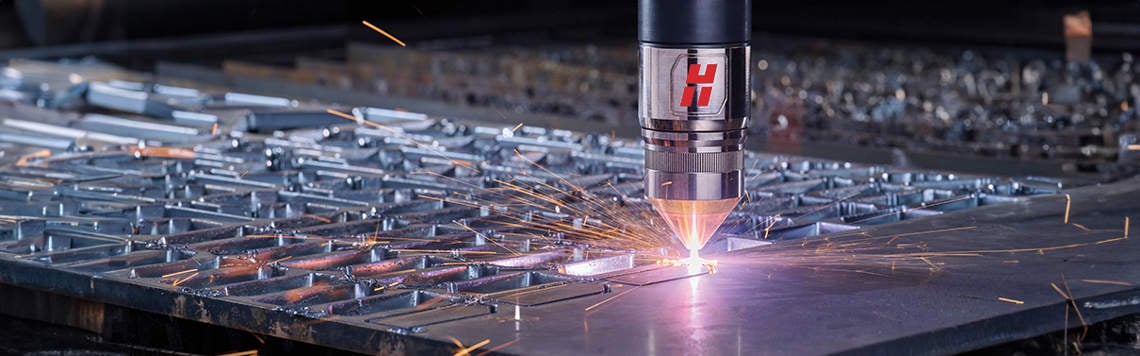
When comparing plasma cutting against laser, plasma excels across a wide range of material thicknesses. It’s especially advantageous when cutting metal greater than 16 mm (5/8”) in thickness as it’s faster, has a lower initial investment and direct operating cost, and is more forgiving when working with imperfect or reflective metal. In addition, high-definition plasma cuts bolt-ready holes and bevels easily.
Benefits of choosing plasma cutting over laser cutting
Plasma and fiber laser are productive industrial cutting technologies with advantages and disadvantages. Choosing which technology depends on the specific job and the cutting outcomes that best fit your requirements. Because it’s a newer technology, fiber laser is sometimes assumed to be superior and more modern. However, while fiber laser has only recently been used to cut metals thicker than sheet gauge, plasma has been perfected over the last several decades to produce high-quality cutting outcomes with low initial investment and operating costs. Most importantly, before selecting which technology is suitable for your operation, it’s vital to consider the following:
-
Material thickness
-
Cut quality
-
Cut speeds
-
Operating cost
-
Initial investment
-
Workpiece condition
-
Maintenance
Plasma produces excellent cut quality
The cut quality difference between X-Definition® plasma technology and laser is small. Hypertherm XPR170® and XPR300® X-Definition plasma deliver a surface finish that’s generally smoother than fiber laser in thicknesses over 16 mm (5/8″) and has consistent edge quality over the life of a consumable set. Combined, X-Definition plasma can achieve cut quality that rivals laser across mild steel, stainless steel, and aluminum.
A helpful reference to compare the two technologies’ cut quality is ISO 9013, an international standard for classifying the quality of parts cut with a thermal process. ISO 9013 classifies a method’s angularity—a measurement of deviation from perpendicular—in ranges from 1 (the least deviation) to 5 (the most deviation.)With a cutting machine offering superior motion capabilities, X-Definition plasma delivers ISO Range 2 cuts on material less than 10 mm (3/8″) thick and Range 3 cut quality on thicker material.
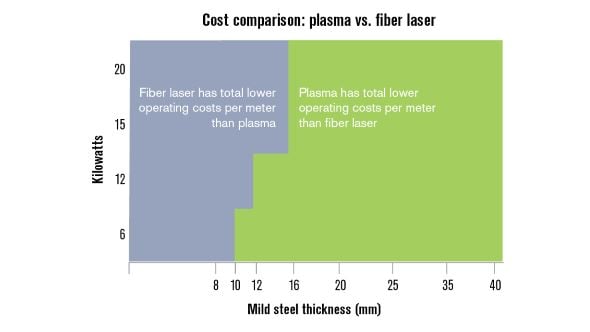
Plasma cuts bolt-ready holes and weld-ready bevels
When paired with CAD/CAM software, like ProNest®, dramatically reduced labor costs and downstream bottlenecks can be achieved. SureCut™ technology applications create high-quality cutting outcomes—while reducing setup and testing—by embedding plasma knowledge and process parameters. This reduces complex programming, trial and error, and operator intervention.
Here’s how SureCut processes help to maximize Hypertherm plasma performance:
-
True Hole® produces more detailed and defined holes with less taper and minimal lead-in and lead-out marks. True Hole creates bolt-ready holes right on the plasma table, eliminating the need to drill holes in a separate step.
-
True Bevel™ applies the correct cutting parameters automatically so operators can cut beveled edges in one pass without needing a second step—often common with competing technologies. Welders no longer need to manually cut or grind beveled edges to a specified angle.
-
Rapid Part™ targets and optimizes process steps considered non-value added. This includes the time the plasma torch needs to retract and move into place and steps like gas pre-flow. By shortening or eliminating non-cutting time, operators can cut more parts—sometimes twice as many—in the same amount of time.
-
Plate Saver™ combines XPR® arc stability and specialized software parameters to increase material utilization dramatically.
Laser tolerances come with cost tradeoffs
The difference between plasma and laser tolerances is smaller than you might think, at roughly 0.25 mm (0.01″) or about the width of a business card. As this article on laser tolerances explains, added tolerances often come with cost tradeoffs. While a fiber laser’s kerf width can be advantageous, it can work against your production flow when cutting thicker metals. Thin kerf can cause parts to easily bind and not release from the skeleton, slowing your production flow and requiring operator intervention.
Plasma is fast
Especially when cutting metals over 16 mm (5/8”), a plasma cuttter is faster than fiber laser. This translates to higher productivity, fewer bottlenecks, better on-time delivery, and greater cash flow and potential for business growth.
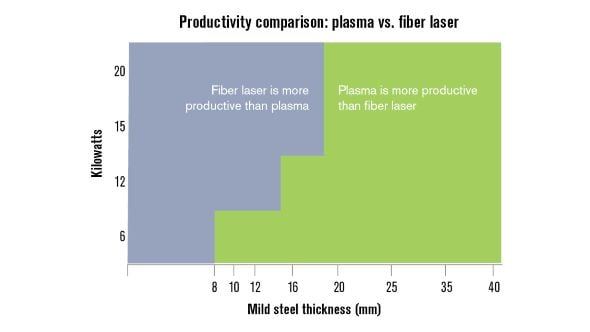
Plasma costs less
Many factors go into the costs for your cutting operations, including gas, electricity, consumables, maintenance, labor, scrap, and the initial investments for the machinery. Ideally, your cutting system will deliver consistent results across the life of the consumables and provide low part-to-part variability over a range of metal types and thicknesses, reducing scrap and finished part costs.
When considering the direct operating costs of a cutting operation, plasma often costs less per foot/meter for thicker metals due to refined processes and reduced gas consumption. Even where fiber laser direct operating costs are lower, as with thin metals, make sure you calculate the electricity consumption and gas consumption requirements of the fiber laser system. Customers are often shocked at the high consumption of these commodities and the need to install bulk gas storage systems or acquire nitrogen generation systems.
The initial investment for a plasma cutting machine is typically 2-5X less than a fiber laser cutting system. While that may seem like a one-time cost, the depreciation charges to your firm’s income statement will significantly increase your fiber laser system's total cost of ownership (TCO) for years to come. Unless your fiber laser machine is cutting at high utilization, it’s unlikely to get a return on your investment.
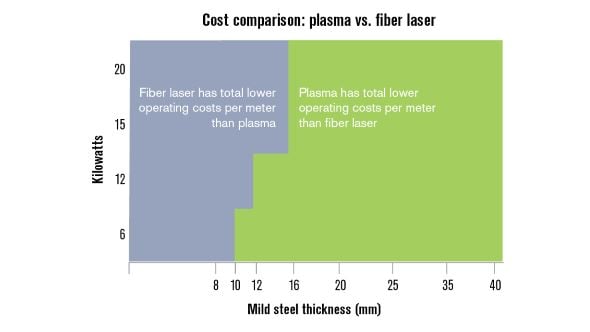
Plasma is versatile
Plasma is highly forgiving of the metal condition being cut. Whether the metal is oxidized, painted, or has variable thickness based on the cut type, plasma reliably makes the cut. Previously, cutting with laser required the plate to be a specific grade, stored inside, and/or cleaned before the cutting operation. While laser’s ability to handle these adverse material conditions is improving, it typically involves additional processing steps like a broad-beam vaporization pass, which lengthens process cycle times.
Plasma is robust and reliable
Time and again, customers report that plasma’s most significant attributes are its simplicity, robustness, and reliability. Maintenance is straightforward, and typically, in-house maintenance departments can easily manage all but the most complex procedures. In the past, CO2 lasers had a reputation for being finicky. They were not reliable, and maintenance costs were high. Fiber laser, with fewer power source components, is markedly more reliable than older laser technologies. Still, maintenance is critical for these machines and requires specialized technicians to inspect, adjust, and maintain the system regularly. Because the cost and delicacy of some components—for instance, a laser cutting head—can cost tens of thousands of dollars, these units are often swapped and returned for repair in a clean room environment.
Recently, many regions have seen the influx of low-cost laser systems promising the best of both worlds: good cut quality and low initial investment. If something sounds too good to be true, it probably is. Ensure you investigate the costs of owning one of these laser systems. Poor service, poor reliability, long lead times for replacement parts, and non-existent customer service may be the price you pay for the initial good deal.