GH Engineering solves structural steel fabrication challenges with X-Definition plasma
Finds success partnering with Hypertherm Associates™ and Plazmax® Technologies
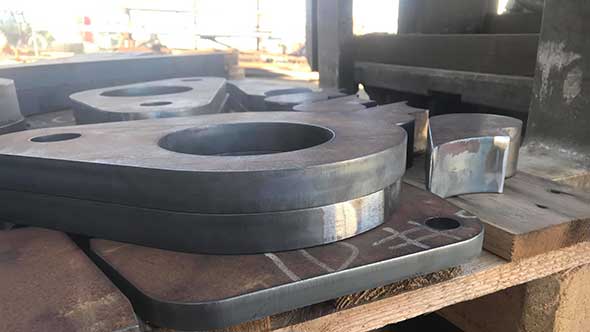
— Business impact —
-
Significantly reduced production time
-
Higher throughput
-
Increased profits
“We took a leap of faith and invested in the larger Plazmax CutPro HS cutting table with the Hypertherm XPR300® plasma system. The decision turned out to be great and enables us to not only handle current jobs well but also be better equipped for faster, bigger, and longer cutting jobs down the road.”
– Gary Hobbs, Managing Director at GH Engineering
Overview
Structural steel is one of the most widely used construction materials of the century and viewed as a crucial component of modern architecture. In some countries, the use of larger, thicker, and heavier structural steel pieces is the norm. Over time, regulators have adjusted governing regulations regarding structural steel usage to ensure occupant safety. To handle these types of materials confidently, fabricators require the right, end-to-end cutting solution.
Situated in Palmerston North and founded in 2007, GH Engineering has several years of experience in architectural and structural metals manufacturing and delivers components to the structural steel and construction industries. To ensure its ability to handle diverse customer needs and have long-term business success, the New Zealand-based metal fabricator needed to ensure it had the right cutting solution in place.
Challenge
As demand for structural steel components grew, GH Engineering saw a corresponding increase in orders for sizable, heavy metal slabs. Although the company had a Hypertherm Powermax105® plasma system from Hypertherm Associates on a light industrial cutting table, the set-up no longer met their needs. It was simply too small. The company cut some of its larger 2D parts on a beamline, designed for 3D cutting, and outsourced the rest. However, outsourcing increased their costs and decreased production control, invariably affecting project timelines.
GH Engineering decided that investing in a new plasma cutting table was the answer. The team began to shortlist options that could expand their in-house capabilities and improve work processes.
When evaluating options, GH Engineering deliberated over key factors that mattered most to structural steel and construction industries, including cut tolerances of acceptable ranges, consistency in cut quality, production runtime, and return on investment.
Solution
The company reached out to Plazmax® Technologies — a manufacturer of CNC profile cutting solutions that exclusively feature Hypertherm’s hardware and software products — to explore some of their advanced automated solutions.
Plazmax understood GH Engineering’s needs well and made a radical recommendation: consider a Hypertherm X-Definition plasma system to help future-proof the fabricator’s business. GH Engineering took their advice and invested in the Plazmax CutPro HS system, fully integrated with Hypertherm Associates’ X-Definition XPR300® plasma system, EDGE® Connect CNC system, and ProNest® CAD/CAM software. This solution suite helped to significantly enhance the metal fabricator’s capabilities and expand the range of services it could offer clients.
GH Engineering now fulfills all cutting jobs internally, while meeting stringent customer requirements. The production team saves the time and effort required to transport 15 to 40 tons of material to and from the external contractor’s site and uses its older beamline to process the 3D parts it was designed for.
The entire suite of technologies has worked well together to enhance GH Engineering’s capabilities. With the consumables lasting longer, it’s no wonder that the machine can achieve longer uptimes to complete jobs much quicker.
Brad Johnston, Product Development Manager
Plazmax Technologies
GH Engineering’s rise in prominence among private and public sectors, facilitated by superb quality and increased offerings, has enabled the company to expand its business to include structural steel businesses throughout the North Island in New Zealand.
Learn how your business can strike the perfect balance between cut quality, cut speed, and cost. Click below, fill out the form, and the right expert will be in touch.
Prefer to research more before having a conversation? Learn more about XPR plasma.