Powermax SYNC, where have you been all my life?
The Boilermakers adopt Powermax SYNC for apprenticeship program and simplify operations
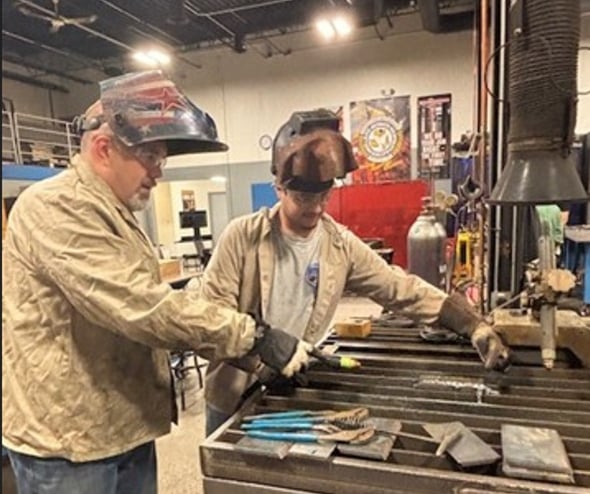
— Business impact —
-
Reduces operating costs by lasting significantly longer
-
Eliminates consumable part mix-up and operator error
-
Achieves dross-free bevels with little to no secondary operations
Apprentice boilermakers learning to weld, gouge, and bevel can be tough on equipment as they develop their skills. As the Administrator of the Boilermakers Northeast Area Apprenticeship, Jason Dupuis is responsible for ensuring his students train on the most reliable machines, and in particular, machines they’ll most commonly use in the field. That’s why Jason depends on Powermax SYNC® for his training schools—they’re cost-effective, easy to use, and provide high-quality cutting.
Boilermakers are vital to construction
The International Brotherhood of Boilermakers’ Union represents over 100,000 workers throughout the United States and Canada. Boilermakers are vital to construction project teams that erect and repair pressure vessels, air pollution equipment, and blast furnaces, to name a few. Apprentices join a four-year program and log 6,000 hours, completing a minimum of 144 hours per year in the shop. They start with the basics on an oxygen hand torch and then progress to plasma cutting, primarily for beveling.
Trusting the process with Powermax SYNC
Before adopting the new Powermax SYNC systems, Jason relied on Hypertherm traditional Powermax plasma cutters, which use a 5-piece consumable. At the start of each new class, Jason would order a surplus of Powermax consumables, only to have instructors call a week later requesting more nozzles. With the understanding that apprentices often load consumable parts out of order or install a swirl ring backwards, he chalked it up to the cost of doing business. That was about to change.
Jason needed two new machines in his shop, and the new Powermax featured a single-piece Powermax cartridge versus his current 5-piece stack-up consumable. With apprentices burning through consumables, Jason was discouraged. His business couldn’t afford to spend more on consumables. With Powermax SYNC, he’d have to replace a whole cartridge instead of single components, such as an electrode, which was often the piece needing replacement. An electrode typically costs $10, while the cartridge costs around $55. He went onto eBay to look for used machines and even wondered if he could put an old torch on a new machine. He decided to call his district sales manager for guidance.
“You want to go with the SYNC. Buy it, use the cartridge,” advised Gordon Snyder, senior district sales manager at Hypertherm. “You're going to like it so much, you're going to call me and order another machine. Trust me on the process.”
Grudgingly, Jason gave the SYNC a try. After the first day, he was a convert.
After the first day of running a Powermax cartridge, I was like, ‘Where have you been all my life?’ This thing lasts 10 times longer than the original consumables. I was blown away.
Jason Dupuis
Boilermakers Northeast Area Apprenticeship
Delivering a longer consumable life, Jason ensures his students spend more time cutting. With an easy-to-use single-piece cartridge versus the traditional five-piece stack-up, the chance of damaging a plate or breaking the torch is significantly reduced. Instead of buying an excess of consumables, Jason now conducts an intensive three-week class with 3 or 4 Powermax cartridges, saving money and streamlining apprentice work.
Boilermakers simplify operations by adopting Powermax SYNC
It became an easy decision for Jason to retrofit all his locations with Powermax SYNC. The single-piece cartridge lasts significantly longer, making it more cost-efficient, eliminates inventory issues in multiple locations, and is easy to use for his students, many of whom are plasma cutting for the first time.
“Mixing up consumable parts from a stack-up is eliminated with Powermax SYNC. Insert the Powermax cartridge, use it until it stops working, and then replace it with a new one,” Jason explained.
Powermax SYNC excels in cutting quality
Apprentices primarily use plasma cutting for bevel cutting, and each cartridge is designed to optimize the cutting or gouging process for the best performance possible. Jason noticed this when he tried the Powermax cartridge.
“You don’t have to hit the bevel part with a grinder before you weld,” he explained. “There’s no dross to knock off. I cut a part, throw it in a pile, and the students grab it and go weld.”
Retrofitting Powermax is easy and cost-effective
Although Jason was initially hesitant to try Powermax SYNC, he was quickly won over once he did. Much of his concern was based on cost and usability. He discovered Powermax SYNC was ultimately more cost-effective and so easy to use that productivity increased. Once they exhausted their original consumable supplies in several locations, they switched to Powermax SYNC.
“To anybody considering switching from the 5-piece consumable stack up to the Powermax cartridge, just do it. You get a better cut, it’s cost-effective, and it couldn’t be easier,” Jason said. “Depending on the age of your machine, you may need to purchase a Duramax torch and torch adapter. Once you have the adapter, turn on the machine, and you’re ready to go.”
Think twice when considering ‘good enough plasma’
Jason ensures that equipment costs for the apprenticeship programs stay in check, but that doesn’t mean less expensive plasma cutters on the market, easily found on Amazon or other online sites, sway him.
Don’t get blinded by price alone. You can always get cheaper equipment, but what happens when your ‘good enough plasma’ system breaks? There’s no one on the other end of the line, and it’s months before a replacement part arrives. Now, you’ve lost time and money in downtime.
Jason Dupuis
Administrator of the Boilermakers Northeast Area Apprenticeship
Other reasons Jason values Hypertherm products are technical support and customer service.
“Gordon is an absolute rock star. If I have any questions, I’ll get a phone call back within minutes. You get what you pay for – in the long run, buying a quality machine like Hypertherm Powermax costs less in every way.”
Busy shops depend on machines that start up every time
Jason, his instructors, and apprentices have relied on Powermax plasma cutters for decades. Powermax plasma cutters, considered the most rugged in the industry, are designed to withstand harsh environments and have a lifespan of over 10 years. He noted that they have a few Powermax systems that are 20+ years old and start up every time.
This 21-year-old Powermax 1650, located at the Albany, NY, facility, is primarily used for cutting welding coupons.
A tool for progress
“The Hypertherm plasma machine is the only machine in the shop that hasn’t been replaced since we opened this training facility. The only change is we started using Powermax cartridges—an absolute game changer for us.”
Jason Dupuis’ experience with the Powermax SYNC is a testament that change can be good! For shop owners and artisans considering retrofitting their older Powermax with a torch adapter or investing in a new Powermax45 SYNC/65 SYNC/85 SYNC/105 SYNC, the time is now. There’s nothing to lose and everything to gain – simplified system operation, streamlined consumable inventory, lower operating costs, and maximum performance.
To learn more about how Powermax SYNC can optimize your cutting operations, visit Powermax SYNC.
For a closer look at the Boilermakers and to learn how to become an apprentice boilermaker, visit here.