The Advantages of Hypertherm Plasma Cutters and CNC Plasma Tables
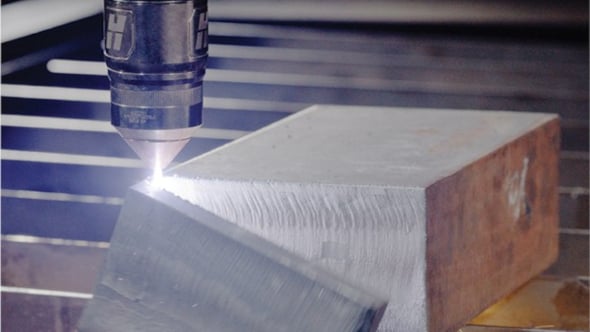
In the world of metal fabrication, precision, efficiency, and reliability are paramount. Hypertherm, a leader in plasma cutting technology, has set the standard for high-performance cutting systems. When paired with CNC plasma tables, Hypertherm systems offer unparalleled benefits that can transform your manufacturing processes and provide you with high-quality cuts.
Why Hypertherm Plasma Cutting Systems Stand Out
1. Precision and Accuracy
Hypertherm plasma cutting machines are engineered to deliver exceptional precision and accuracy, even with high speed cutting. The advanced technology ensures precise cuts and smooth, reducing the need for secondary operations such as grinding and finishing. This level of precision is crucial for industries where tight tolerances are required, such as aerospace, automotive, and metal art.
2. Cutting Speed and Efficiency
One of the standout features of Hypertherm systems is their impressive cutting speed. Faster cutting speeds translate to higher productivity, allowing manufacturers to produce more parts in less time. This efficiency is particularly beneficial for high-volume production environments where time is of the essence.
3. Durability and Reliability
Hypertherm systems are built to withstand the demands of industrial use. The robust components and high-quality materials ensure that the systems can operate reliably over long periods. This durability reduces maintenance costs and minimizes downtime, leading to increased operational efficiency.
4. Ease of Use
Hypertherm systems are designed with the user in mind. The intuitive interfaces and advanced features make them easy to operate, even for those who are new to CNC plasma cutting. This user-friendly design helps reduce the learning curve and allows operators to achieve optimal results quickly.
5. Versatility
Hypertherm systems are versatile and can handle a wide range of materials and thicknesses. Whether you're cutting mild steel, stainless steel, aluminum, or other conductive metals, Hypertherm systems provide consistent clean cuts and high-quality results. This versatility makes them suitable for various applications, from at-home hobbyist cutting to heavy industrial manufacturing.
Benefits of CNC Plasma Tables
When Hypertherm systems are integrated with CNC plasma tables, the benefits are amplified. CNC plasma tables offer several advantages that enhance the overall cutting process.
1. Repeatable Accuracy
CNC plasma tables ensure that each cut is consistent and precise. The computerized x-y controls and torch height controls allow for repeatable accuracy, which is essential for producing parts that meet exact specifications. This consistency reduces material waste and provides accurate cuts - improving the overall quality of the finished workpiece.
2. Automation and Efficiency
The automation capabilities of CNC plasma tables streamline the metal cutting process. Once the cutting parameters are set, the table can operate with minimal human intervention. This automation increases efficiency and reduces the likelihood of human error, leading to higher productivity and better-quality cuts.
3. Versatility in Applications
CNC plasma tables are highly versatile and can be used for a variety of applications. From intricate metal art designs to large-scale industrial projects, these tables can handle diverse cutting tasks. The ability to cut different materials and thicknesses makes CNC plasma tables a valuable asset in any fabrication shop.
4. Cost-Effectiveness
By minimizing material waste and reducing the need for secondary operations, CNC plasma tables can significantly lower production costs. The precision and efficiency of the cutting process lead to better resource utilization and cost savings. Additionally, the durability of Hypertherm systems ensures that the investment in CNC plasma tables pays off in the long run.
5. Enhanced Safety
CNC plasma tables are designed with safety features that protect operators during the cutting process. The enclosed cutting area and automated controls reduce the risk of accidents and injuries. This focus on safety is crucial in maintaining a safe metalworking environment and ensuring the well-being of employees.
Advantages of SYNC Cartridges for a CNC Plasma Table
Hypertherm's Powermax SYNC cartridges bring a new level of innovation and efficiency to plasma cutting. Here are some of the key advantages:
1. Simplified Operation
SYNC cartridges feature a single-piece design that simplifies system operation. The easy-to-identify, color-coded cartridges eliminate parts confusion and streamline consumable inventory management. This simplification reduces downtime and troubleshooting, making the cutting process more efficient.
2. Smart Technology
The RFID-enabled SmartSYNC torches and cartridges automatically set the correct amperage and operating mode, eliminating setup errors. This smart technology ensures optimal performance and reduces the likelihood of operator mistakes.
3. Enhanced Productivity
SYNC cartridges are designed to provide up to twice the life for hand cutting and improved quality over their lifespan in mechanized setups compared to standard consumables. This extended life reduces the frequency of cartridge changes, leading to increased productivity and lower operating costs.
4. End-of-Life Detection
SYNC cartridges come with end-of-life detection, which notifies the operator when it's time to change the cartridge. This feature helps maintain consistent cutting quality and prevents unexpected downtime.
5. Data Tracking and Analysis
The advanced torch communication allows for automated process setup and provides access to cartridge data for performance tracking. Operators can analyze usage patterns, such as starts, transfers, and plasma arc-on time, to optimize cutting processes and improve efficiency.
6. Versatility
SYNC cartridges are compatible with various torch styles and application-specific consumables, making them suitable for a wide range of cutting and gouging tasks. This versatility ensures that you can tackle different jobs with ease and achieve the best results.
Advantages of XPR Systems for CNC Cutting
Hypertherm's XPR systems represent the next generation of plasma cutting technology, offering several significant advantages:
1. Industry-Leading Cut Quality
The XPR systems feature X-Definition™ technology, which enhances cut quality on mild steel, stainless steel, and aluminum. This technology ensures cleaner, sharper, and more consistent cut edge quality across a wide range of thicknesses.
2. Optimized Productivity and Reduced Operating Costs
XPR systems are designed to improve productivity with faster cutting speeds and longer consumable life. The advanced power supply technology delivers rapid system feedback, automatically intervening to eliminate events that negatively impact system efficiency and consumable life.
3. Enhanced System Monitoring and Diagnostics
XPR systems come with advanced diagnostic capabilities, including refined diagnostic codes and enhanced system monitoring information. This feature reduces troubleshooting time and provides proactive maintenance data, ensuring optimal system performance.
4. Ease of Use
The XPR systems are designed for intuitive operation with features like EasyConnect™ torch lead and one-hand torch-to-receptacle connection for fast and easy change-outs. The automatic system monitoring and specific troubleshooting codes further enhance ease of use.
5. Increased Versatility
XPR systems are versatile, capable of handling a wide range of applications from thin to thick materials. The systems' ability to deliver superior cut quality on various metals makes them suitable for diverse industrial applications.
Additional Considerations for Hypertherm CNC Plasma Tables
1. Operational Expenses and Productivity Gains
When evaluating a new CNC plasma cutting table, it's essential to consider operational expenses and productivity gains. Hypertherm systems offer faster cut speeds, fewer secondary operations, and improved material usage, which can drive purchasing decisions. Additionally, new technology often provides better energy efficiency, superior cut quality, and longer consumable life.
2. Impact on Employees and Customers
Investing in high-quality equipment like Hypertherm systems can positively impact both employees and customers. For employees, having reliable and easy-to-use tools can increase job satisfaction and reduce turnover. For customers, improved service quality and faster delivery times can enhance loyalty and encourage repeat business.
3. Business Growth and New Opportunities
Upgrading to advanced CNC plasma cutters can open up new business opportunities. With better equipment, you can take on more complex projects, improve product quality, and expand your service offerings. This growth potential is crucial for staying competitive in the market.
Hypertherm Plasma: Your best option for mechanized cutting
Hypertherm systems and CNC plasma tables are a powerful combination that can revolutionize your metal fabrication processes. The precision, efficiency, and versatility of Hypertherm systems, coupled with the automation and consistency of CNC plasma tables, provide a cutting solution that meets the demands of modern manufacturing. By investing in these advanced technologies, you can enhance productivity, reduce costs, and achieve superior quality in your cutting operations.